回顾过去五六十年,先进逻辑芯片性能基本按照摩尔定律来提升。提升的主要动力来自三极管数量的增加来实现,而单个三极管性能的提高对维护摩尔定律只是起到辅佐的作用。随着SOC的尺寸逐步逼近光罩孔极限尺寸(858mm2)以及制程的缩小也变得非常艰难且性价比遇到挑战, 多芯片封装技术来到了舞台的中心成为进一步提升芯片性能的关键。覆晶键合技术已然成为先进多芯片封装最重要的技术之一。
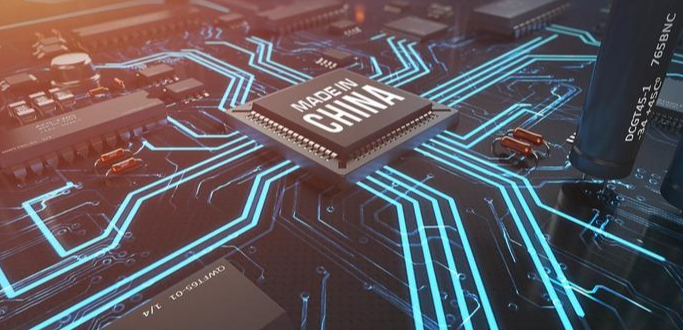
尽管某些基于晶圆级或者面板级扇出型封装的工艺流程可以不用到覆晶封装,但是这个技术方向有其自己的应用局限性。比如其目前量产重布线层的层数大多在五层以内,使其不太适合服务器芯片的封装。如今最常见的基于焊球的覆晶键合封装技术一共有三种:回流焊(mass reflow), 热压键合(Thermo Compression Bonding or TCB)和激光辅助键合(Laser Assisted Bonding, or LAB)。基于铜铜直接键合的覆晶封装不在这个文章的讨论重点,我们会在后续的文章中讨论目前最具希望能进一步缩小的bump间距(bump pitch scaling down)的方法,比如混合键合(Hybrid bonding)和铜铜直接热压键合等等。
热压键合工艺的基本原理与传统扩散焊工艺相同,即上下芯片的Cu 凸点对中后直接接触,其实现原子扩散键合的主要影响参数是温度、压力、时间. 由于电镀后的Cu 凸点表面粗糙并存在一定的高度差,所以键合前需要对其表面进行平坦化处理,如化学机械抛光(chemical mechanical polishing,CMP),使得键合时Cu 表面能够充分接触. 基于目前研究文献,通过热压键合工艺实现Cu-Cu 低温键合的方法从机理上可分为两类,即提高Cu 原子扩散速率和防止/减少待键合Cu 表面的氧化.表一在high level总结了这三种基于焊球的覆晶键合封装技术的优缺点。 可以看到没有一种键合方式是完美的。对于某个产品来说,任务是要找到最合适的键合方法。作为本文的重点,热压键合最大的优势是对die和基板(可以是substrate, another die or wafer or panel)的更为精准的控制。
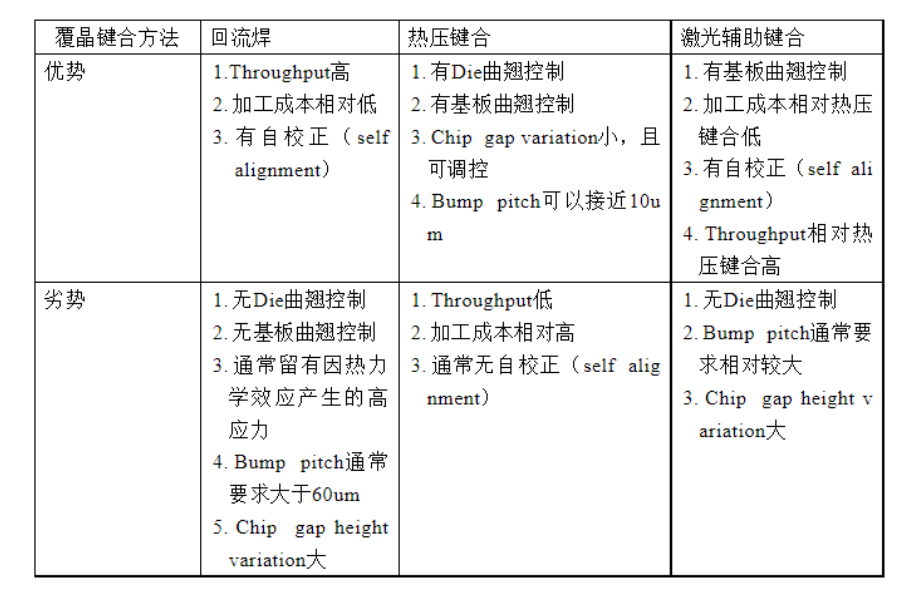
表一:基于焊球的覆晶键合技术
接下来我们着重讨论一下高端的逻辑芯片的键合方式为什么逐步从回流焊键合过渡到热压键合。图一(a)给出了一种常见的回流焊芯片键合流程。先将芯片上的bumps沾上助焊剂(flux)或者在基板上的C4 (controlled-collapse chip connection)区域喷上定量的助焊剂。然后用贴片设备将芯片相对比较精准地放到基板上。然后将芯片(die)和基板整体放到一个回流焊炉子里。常见的回流焊的温度控制由图一(b)给出。整个回流焊的时间通常在5到10分钟。虽然时间很长,但因为这是批量处理,一个回流焊炉同时可以容纳非常大量的加工产品。所以整体的吞吐量还是非常高的,通常可以达到每小时几千颗芯片的产量,或者更高。
先进芯片封装清洗:
合明科技研发的水基清洗剂配合合适的清洗工艺能为芯片封装前提供洁净的界面条件。
水基清洗的工艺和设备配置选择对清洗精密器件尤其重要,一旦选定,就会作为一个长期的使用和运行方式。水基清洗剂必须满足清洗、漂洗、干燥的全工艺流程。
污染物有多种,可归纳为离子型和非离子型两大类。离子型污染物接触到环境中的湿气,通电后发生电化学迁移,形成树枝状结构体,造成低电阻通路,破坏了电路板功能。非离子型污染物可穿透PC B 的绝缘层,在PCB板表层下生长枝晶。除了离子型和非离子型污染物,还有粒状污染物,例如焊料球、焊料槽内的浮点、灰尘、尘埃等,这些污染物会导致焊点质量降低、焊接时焊点拉尖、产生气孔、短路等等多种不良现象。
这么多污染物,到底哪些才是最备受关注的呢?助焊剂或锡膏普遍应用于回流焊和波峰焊工艺中,它们主要由溶剂、润湿剂、树脂、缓蚀剂和活化剂等多种成分,焊后必然存在热改性生成物,这些物质在所有污染物中的占据主导,从产品失效情况来而言,焊后残余物是影响产品质量最主要的影响因素,离子型残留物易引起电迁移使绝缘电阻下降,松香树脂残留物易吸附灰尘或杂质引发接触电阻增大,严重者导致开路失效,因此焊后必须进行严格的清洗,才能保障电路板的质量。
推荐使用合明科技水基清洗剂产品。